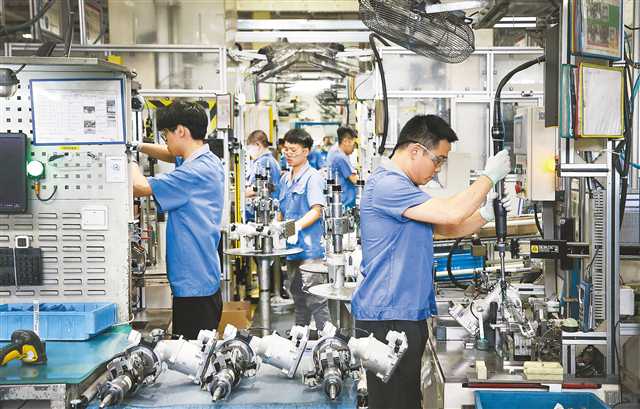 |
十月十一日,重庆耐世特转向系统有限公司,员工正在总组装线上加紧生产。特约摄影 钟志兵/视觉重庆 |
编者按
近日,重庆印发《关于推进制造业亩均论英雄改革的指导意见》,明确提出要以亩均效益改革引领推动制造业提质增效。事实上,“亩均论英雄”不仅是制造业转换增长动力的重要抓手,也是经济实现高质量发展的关键一招。
本报今起推出“寻找重庆亩均英雄”系列报道,寻访重庆那些“内功”深厚的工业园区、楼宇、商圈、企业,看它们在提升“亩均效益”上取得了怎样的成绩、探索出哪些好做法、有哪些经验启示,敬请关注。
行业亩均产值500万—600万元,这家公司为8752万元;
行业人均产值50万—60万元,这家公司为355万元。
这家公司,就是位于江津德感工业园的重庆耐世特转向系统有限公司(简称重庆耐世特)。重庆耐世特究竟有何高明之处,无论亩均产值还是人均产值,都远远高于大多数同行?
“我们从来没让客户失望过”
今年上半年,重庆耐世特派出20多人的研发团队前往苏州总部。
此行,他们只有一个目的,就是学习研究如何满足新能源汽车客户对更大助力产品的需求。
现在,汽车厂商提升产品竞争力,越来越在意产品性能细节。重庆耐世特公司总经理龙宏彬表示,公司研发团队通过不断优化设计,已经迭代出了第8个版本的技术方案,“我们从来没让客户失望过。”
从提供产品,到提供全套解决方案,这是重庆耐世特越来越强大的核心竞争力。比起单纯的产品供货,提供解决方案也创造了更高的附加值和利润。
在重庆耐世特样品陈列台前,龙宏彬向记者展示了一款最新产品——REPS(齿条式电动助力转向系统)。这个一米多长,看上去像“架子”似的汽车部件,目前全球范围内能做出来的公司屈指可数,也是各汽车品牌眼中的“刚需”产品。
龙宏彬介绍,REPS是CEPS(管柱式电动助力转向系统)的升级版,能够满足新能源汽车等大级别、大重量乘用车的安全性、舒适性要求。该产品将机械、传感、电控、软件、人工智能等方面的技术,融合到一个完整的解决方案中,研发制造难度极大。
重庆耐世特的产品技术优势是如何建立的?
龙宏彬表示,公司由耐世特中国和重庆建设工业合资成立,在产品研发上,依托耐世特百年技术积累,形成了全球、亚太和重庆的三级研发体系。
目前,该公司54%的员工都是研发人员,公司先后荣获国家高新技术企业、重庆市中小企业技术研发中心、重庆市数字化车间、长安汽车优秀供应商、通用汽车供应商质量卓越奖等一系列荣誉。
整个车间找不出多余空地
工业企业亩均产值要高,必须通过集约布局、精益生产,向空间要效益。
10月18日,记者进入重庆耐世特的生产车间,第一感觉就是紧凑。
加工机、货架、机械臂、传送带等设备一个挨着一个,摆放密集,整个车间几乎找不出多余的空地。这里无论是设备布置,还是工位安排,都做到了空间上的极致应用,不留死角。
“我们在最初设计制造工艺和生产流程时,就考虑到各个工序、环节的高效承接,避免人力物力在距离和时间上的浪费,以及各个工区间的互相干扰。”龙宏彬表示,此外,生产线布局也是根据材料、加工和装配实际需求来灵活调整,从而实现最高效率。
重庆耐世特的工厂总面积为8000平方米,其中办公区2000平方米,生产区仅4000平方米,但却创造了13亿元的年产值。
现在,重庆耐世特还要来一次“极限挑战”。
龙宏彬介绍,公司计划引进一条价值2亿元的新生产线,可以选择新建厂房,或布置到现有厂房里。“新建厂房,设备用地能有更多余裕空间,但建厂房至少要花五六千万元,需要一到两年时间。”龙宏彬说,关键是这与公司精益生产的理念不符。
于是,他们计划把新生产线“塞”进现有厂房剩下的2000平方米空间内。
难度很大,现在该公司正忙着做产线的引进规划和布置,方案已经讨论和优化了30多个版本。龙宏彬很有信心地表示,这个项目做下来,公司在机加工行业亩均产值方面,稳坐第一把交椅。
数字化渗透到工厂每个角落
目前,重庆耐世特一个月要交付10万套左右的产品,生产线长期处于满负荷状态,今年中秋国庆假期,工厂仍在加班加点生产。
如何提升生产效率,确保稳定供货?重庆耐世特让数字化和智能化来帮忙。
10月17日下午,重庆耐世特车间,负责涡轮零部件生产的工位上,机械臂正在三个不同的工作台间来回“倒腾”,忙个不停。
“以前,这里由一位工人负责三个工作台,工作强度非常大,现在只需要一台机械臂就搞定了。”车间负责人介绍。
工位旁边的显示屏上,密密麻麻的数据不断跳动,机械臂和工作台设备的所有操作,都被传感器完整地记录下来,并上传到现场的生产管理系统里。
这个系统还“吃”下了工厂里每个产品、每台设备、各种工艺、各站点以及生产线的所有数据。分析这些数据,就可以得到当前的产出趋势,并发现问题加以改进。
“比如某一台设备出现故障,过去我们要详细询问员工发生了什么,而现在只要手指一点,马上就知道了。”龙宏彬在手机上操作着这个系统。“这套系统每天都会产生20G以上的数据,帮助我们进行工艺调整,并优化各项流程和管理。”
重庆耐世特从2016年开始做这套数字系统,每年都要迭代,回报也很明显:设备综合效率提升了20%以上,年直接综合效益达3000万元以上。
不但生产自动化、物流智能化,该工厂的问题件也实现智能追溯,包括问题分析、整改效果评估、跟踪验证等。可以说,数字化已经渗透到了工厂的每一个角落。