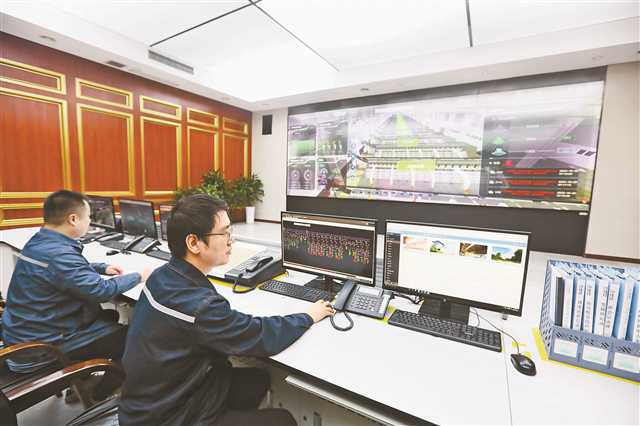 |
10月20日,旗能电铝总控室,数字孪生工厂通过三维建模,对工厂设备和整体环境进行可视化呈现,实现“所见即所得”。记者 罗斌 摄/视觉重庆 |
“1003号电解槽数据异常!”10月20日,位于綦江的重庆能源旗能电铝总控室,大屏幕上的数字地图上,电解车间出现了一个醒目的红色信号。工作人员立刻将数字地图放大,车间的所有电解槽出现在画面上。
屏幕右下方框内,鲜红色文字高频闪烁,显示问题电解槽上的各个传感器所捕捉到的数据。总控室工作人员在电脑上按了一个键,画面迅速切换到了这个电解槽周边的摄像头,呈现出电解槽运行实况,同时,这位人员按照预案发出处置指令,不一会儿就看到两名技术人员,前往处置。
总控室工作人员将数据系统采集到的各种异常信息、分析结果报给在现场处置异常情况的技术人员,帮助他们判断问题所在,不一会儿,异常情况处置成功,报警消失。
“这就是数字工厂的强大之处。”旗能电铝副总经理、总工程师王民表示,过去车间出现异常情况,现场人员发现后,要先排查整个区域的设备,并通过一些详细的检查测试,才能够了解到异常发生的具体点位和异常发生原因,可能会因为处理不及时导致风险。
“如今,我们在数字孪生工厂的帮助下,实现了所见即所得,虚拟和现实的融合,极大提高了生产和安全管理的效率和精度。”王民说,数字孪生工厂,就是通过三维建模,对工厂设备和整体环境进行可视化呈现,且通过摄像头和各种控制器,实现虚拟和现实的“无缝切换”。目前,相关的数字技术正在旗能电铝的各个方面发挥重要作用。
王民介绍,旗能电铝现在一共构建了10多个数字应用场景,用以提升安全和效率。例如,电解铝的电解槽加料通道经常会堵塞,过去主要靠人工巡视和疏通,但这里的作业环境温度高达60℃—70℃,人工巡视和疏通非常辛苦。如今采用数字控制,如果发现物料不够畅通就会停止下料,并通过气缸加压疏通,大大降低了人工强度。
该工厂还建设了数字测温系统,在5000-6000个重点风险点位开展自动测温,传感器几秒钟就可以测一次温,数据全部通过5G传输,该系统应用几年来,工厂没有发生过一起漏槽险情。
(本报记者 白麟)