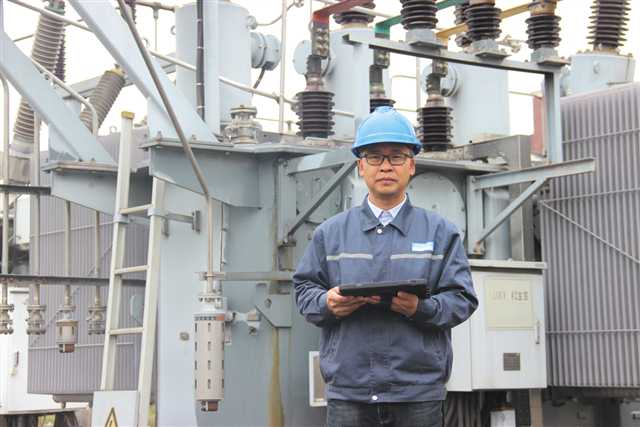 |
杜伟巡查工厂变配电系统 |
2023年重庆五一劳动奖章获得者、贝卡尔特(重庆)钢帘线有限公司维修经理杜伟,自2008年入职后,一直扎根生产基层,认真务实地深耕设备维修维护领域,持续不断地进行技术和管理创新。通过创新,让企业产品更加稳定,在激烈竞争的市场上,更加有竞争力;通过创新,让工厂运营成本持续可控降低,助力企业的可持续发展。
助力节能减排,创建绿色低碳工厂
为了积极响应国家碳排放/碳中和战略,如期达成“双碳”目标,作为工厂能源管理一线负责人的杜伟,2022年在工厂范围内,导入了“节能减排,低碳未来”的绿色制造理念,组织了贝卡尔特重庆工厂的“节能减排和可持续发展项目”活动,通过和集团以及工厂技术部门协作,识别出了7种系列产品的生产工艺过程存在巨大的能耗节约空间,完成全部产品系列的生产设备改造后,预计每年将为工厂带来超过500万千瓦时的电能节约。
同时,杜伟和集团设备开发部门一起,测试并成功引入超高效电机在钢丝拉拔设备上的应用,全部改造完成后,预计将为工厂带来超过350万千瓦时每年的电能节约。
在集团内部协作开发节能减排项目的同时,杜伟积极引入外部力量参与工厂节能减排项目识别和开发,通过和空压机厂家合作,在分析空压机能耗数据后,及时的调整并优化了空压机布局,提升了空压机单位能耗效率。功率因数是衡量电能使用效率的关键指标,提升功率因数不仅可以提高电能效率,节约电能,还可以减少谐波对电网的冲击,提升供配电系统的稳定性和安全性。
在工厂开展“节能减排和可持续发展项目识别”活动期间,杜伟邀请专业的功率因数补偿设备厂商,到工厂实地测量谐波产生的具体情况,定制功率因数补偿设备和技术方案,并制定了逐年功率因数补偿设备的投资计划。
通过“节能减排和可持续发展项目识别”活动的开展,杜伟及同事们共识别出了62条能源节约项目,14条节水项目。其中62个能源节约项目,预计将带来1496万千瓦时每年的能源节约,降低工厂能源消耗强度16.9%,预估将降低1.4万吨二氧化碳排放,达成了集团公司为工厂设定的2030年前15%能源消耗强度降低目标;14个水资源节约项目,将带来22万立方米水资源节约,达成2030年前25%水资源节约目标。
在组织识别节能降耗项目的同时,杜伟积极推进已识别的节能减排项目立项,预算申报和实施落地,为能耗双控目标达成,创建绿色低碳工厂献计献策,得到工厂各层级高度认可和评价。
围绕“三个维度”对设备柔性化改造
作为工厂维修一线负责人,在做好工厂设备设施和能源综合管理的同时,为了满足工厂在不同产销情景下的生产需求,杜伟和同事潜心研究设备柔性化改进,以自动化和信息化为支撑,从3个维度对设备进行了柔性化改造。
第一个维度,为了降低设备操作复杂度,将设备原装的英文界面进行汉化改造,汉化后的人机界面更加易学易懂,操作更加可靠和高效。
第二个维度,通过对工厂设备布局的研究和优化,对产品生产过程和物料运输特性进行梳理,开创了由工厂本地维修人员直接进行设备布局调整的先例,优化了工序间在制品转运路线,降低了叉车物料转运负荷和工作人员无效走动时间,同时,减少了叉车和人员交叉工作的频率,提升了整体生产效率和安全性。
第三个维度,为了减少设备对生产工艺和计划安排的限制性因素,更新了钢丝初拉设备卷筒,提升了粗拉设备对钢丝的整体拉拔能力。通过对电镀生产线钢丝淬火工序设备改造,提高了设备淬火温度调节范围和稳定性能,大幅扩展了一机多用的能力,大幅降低了实际生产成本。
杜伟开拓性地创造了设备预测性动态维修的模式,利用生产设备运行过程中不同部位的振动特征,温度特性和电压电流动态变化曲线,通过振动检查仪和温度电压电流记录仪,在线收集设备运行过程参数和信号,分析设备运转情况,定制设备维修策略和计划,有针对性地进行修理,从而减少设备停机时间,避免维护不当导致的经济损失,提高了设备全寿命周期的综合利用率和可靠性,该模式被贝卡尔特中国区其他工厂广泛采用。
期间,杜伟引进设备热成像检查技术,利用不同温度条件下物体表面的红外热成像差异,对工厂供配电系统进行定期的在线热成像检查,发现供配电线路、接点的温度变化异常后,极早介入并消除系统缺陷。通过红外热成像技术应用,多次有效地防止电气火灾的发生,为工厂持续稳定安全运行贡献了自己的力量。
刘敏 潘锋 图片由贝卡尔特(重庆)钢帘线有限公司工会提供