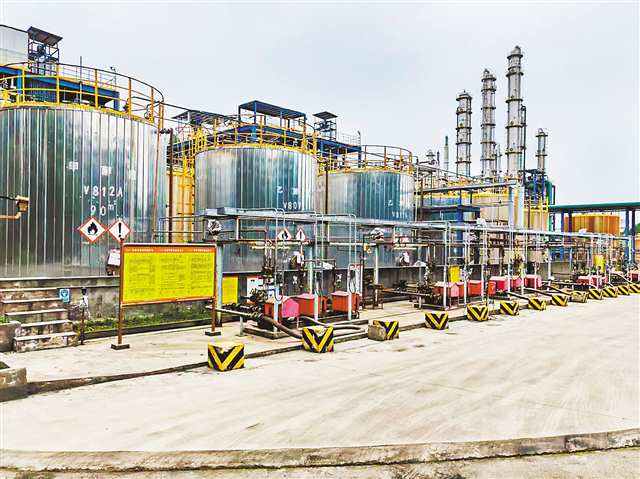 |
重庆中邦科技有限公司生产线。(受访者供图) |
在传统观念中,化工产业利润增长常常难以摆脱环境成本的羁绊。
然而,来自万州的重庆中邦科技有限公司(以下简称中邦科技)却颠覆了这一“刻板印象”,凭借修炼“绿色炼金术”,不仅在生产过程中实现了能耗与废弃物排放的“断崖式”削减,更驱动年利润率飙升45%。
加氢法重塑生产逻辑
4月10日,记者来到万州经开区的中邦科技厂区,看到了中邦科技的核心产品之一——2,3-二氯吡啶。这是一种外观平平无奇的白色晶体,却在现代医药和高效农药的精密合成中扮演着“关键骨架”的角色。
该公司总经理孔青明介绍,许多疗效显著的药物分子,其核心结构都离不开吡啶环,2,3-二氯吡啶就是搭建这些复杂结构的重要基石。在农业领域,它是合成某些新一代高效、低毒杀虫剂不可或缺的起始原料。
近年来,随着国内生物医药等市场的繁荣,2,3-二氯吡啶需求暴增,产品供不应求。然而对于很多化工企业来说,生产代价也不小。
“过去,业内生产2,3-二氯吡啶普遍依赖的是‘烟酰胺降解法’。”孔青明介绍,这套技术就如同“漫长而曲折的跋涉”——该方法以烟酰胺为起点,需经过4大步、19道细分工序,流程冗长复杂。
其弊端也十分明显:首先是效率低下且选择性差,副产物多导致分离困难,总收率仅50%—70%;其次是涉及不稳定的重氮盐,存在安全风险。更关键的是环境负荷巨大,每生产一吨产品,就会伴生约40吨废水和8吨固体废弃物。
处理这些“三废”,花费巨大。“比如一个生产批次大约700公斤产品,光是处理废水(约30吨,处理费9000元)和固废(约6吨,处理费12000元),成本就要21000元,再加上能耗,成本超过5万元。”孔青明说,这种生产方式根本赚不到钱。
中邦科技决心闯出新路。公司研发团队历时三年攻关,于2019年取得实质性进展,并工业化应用了“加氢法”这一原创技术,最近几年技术越发成熟。
“加氢法”以2,3,6-三氯吡啶为原料,利用特定的钯碳催化剂,如同精准的“分子手术刀”,只需要一步反应,就直接得到目标产物2,3-二氯吡啶。
“听起来很简单,但关键在于催化剂的选择,这是技术难点,也是我们耗费心血攻关的重点。”孔青明说,这中间经历了无数次的试验、失败与调整。
这项行业首创的技术,带来的效益是革命性的。
首先,生产成本断崖式下降:能耗降低超60%;“三废”处理成本降低95%以上,其中固废几乎实现零产生,废水产生量减少90%。综合下来,每生产700公斤产品,就能节省成本约4万元。
其次,工艺简化,产品收率提升至80%以上。
最后,源头大幅减排,避免了危险的重氮化步骤,提升了本质安全水平。
将单批次效益放大,经济影响更为惊人。“我们今年目标年产3000吨2,3-二氯吡啶。仅成本节约一项理论上就可达1.7亿元以上。这为公司预测年利润率提升45%提供了坚实基础。”孔青明透露。
系统优化让绿色效益“积少成多”
中邦科技的绿色实践并未止步于核心工艺的突破,而是展现出系统性的优化思维,从每一个环节挖掘“绿色潜力”。
例如,该公司投入30万元对产品精馏塔进行了升级改造,用连续精馏替代了能耗高、效率低的间歇操作。这次改造如同将“烧开水”模式变为“温泉”模式,能量利用更平稳高效:每吨产品蒸汽单耗降低约3吨,电耗降低约100千瓦时,月产量提升约50吨,全年直接降本约251万元。
余热还可回收利用:成品精馏产生的大量热蒸气被收集在特制的余热罐中,再作为其他工序的热源使用,就如同“用煮饭的蒸汽再炖个汤”,每一分热量都物尽其用。
这些配套的节能措施,与核心的加氢法工艺相辅相成,共同强化了中邦科技的绿色制造基础。
一张贯穿始终的“绿色成绩单”
中邦科技的绿色发展成效不限于一域,而是贯穿于企业运营的方方面面。
在土地集约利用上,公司厂区容积率(0.65)和建筑密度(40.24%)均优于国家标准,2024年单位用地面积产值高达30.89亿元/平方公里,远超区域平均水平,实现了高效产出。
在原料源头管控上,中邦科技严格执行绿色采购,与供应商签订质量与绿色承诺,建立评价体系,确保原材料安全无害。同时,新工艺的应用使所需原材料种类从15种减至9种,直接减少了物料消耗和潜在风险。
在生产过程洁净化方面,公司加大投入,废气处理设施高效运行,主要污染物排放浓度远低于国家标准的5%,氮氧化物甚至未检出。废水首先在内部循环利用至少10个周期,少量外排废水经专业处理后回用,2024年废水回用率高达82%,最终外排指标同样远低于标准的5%。
孔青明介绍,该公司已设立能源管理中心,实施精细化管理,2024年单位产值能耗(0.54tce/万元)远低于重庆市行业平均水平(0.82tce/万元),单位产品取水量(10.6立方米/吨)优于行业水平(12立方米/吨)。