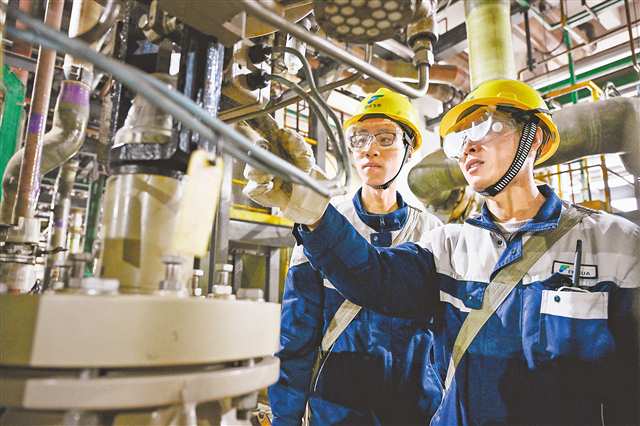 |
2月5日,长寿区飞华环保,工人们正在巡检生产设备,确保生产安全。记者 张春晓 摄/视觉重庆 |
“新年好!”2月5日,春节假期后上班第一天,长寿经开区飞华环保氯化氢回收利用项目车间内,长寿飞华环保有限公司(以下简称“飞华环保”)董事长李定山前来看望慰问一线工作人员。
“项目9台电解槽全部满负荷运转,30名一线员工也已全部返岗,我们实行三班两倒开启正常生产。”项目车间负责人侯兵说。
长寿飞华环保是重庆巴斯夫MDI(一种主要用于合成革、弹性纤维、黏合剂等产品生产的新材料)产业链配套企业,每年可帮巴斯夫处理23万吨氯化氢废气。电解后的氯化氢生成氯气,再作为原料源源不断地输送至巴斯夫MDI项目基地。
23万吨氯化氢尾气如何排
现场,设备轰鸣,工人们戴着手套,小心翼翼地调试阀门,核对压力、压强等运行参数。“装置投用后解决了巴斯夫酸性废气处理的难题,让前端MDI产能大幅提升。”李定山说。
早在2010年,德国化工巨头巴斯夫看中长寿丰富的天然气资源,将年产40万吨的MDI项目落户长寿经开区,计划在这里建设世界最大的MDI生产基地。然而装置建成后,废气氯化氢的处置却成为最棘手的难题。
氯化氢不能直接排放,传统处理方法是将其溶解于水生成盐酸,再卖给下游市场。但巴斯夫产能太大,下游市场根本无法消化,无奈之下他们只能降低前端产能。李定山告诉记者,“在很长一段时间里,巴斯夫MDI生产装置平均开工负荷基本维持在40%左右,造成了资源浪费。”
经过研讨,最佳解决方案是引进德国技术,将氯化氢电解为水和氯气,水直接排掉,氯气则作为巴斯夫生产MDI的原料循环利用,既解决了废气处理问题,又节省了一笔原料成本。飞华环保承担下这一艰巨的任务。
项目筹建时,面临的最大问题就是人才紧缺。期间,他们多次前往北京理工大学、哈尔滨工业大学、西南大学等高等院校,吸纳招引关键性技术人才。可当时飞华环保还是一家新公司,很少有年轻人才愿意加盟。正当他们一筹莫展时,长寿区推出优才计划,这才吸引到一批优秀人才。
随即,他们组建起20多人的核心团队。2017年,一期9个电解槽陆续投用,具备将23万吨氯化氢废气转化为18万吨氯气的年处置能力。
近20道环节实现国产化替代
“这几年,我们迎难而上,不断消化引进国外先进技术,推动技术国产化改造,整套氯化氢装置有近20道环节实现了国产化替代。”侯兵说。
氯化氢具有极强的腐蚀性,设备容易磨损。一次,一台电解槽的隔热器出现问题,需要更换。他们向德国厂商发出售后要求,得到的回复是:库存有限,至少20周才能发货。
进口隔热器附着着一层特殊的抗腐蚀材料,当时国内没有替代产品。除了等待,他们也想不出更好的办法。“期间我们只能被迫关停一部分产能,损失很大。”侯兵回忆道。
这次经历让飞华环保坚定进行国产化改造,隔热器成为了突破口。一次行业大会上,飞华环保与一家国内材料商达成合作,进行隔热器联合开发。经过反复试验,研发团队最终锁定了碳化硅这种新型材料,并顺利将其用在了装置的隔热器上。
国产化替代不仅逐步解决了技术难题,也节约了大笔生产成本。譬如,原装设备中的压缩机全部采用德国西门子技术,每六年就要更换一次,花费高达800万元,而现在他们通过自主研发,已生产出符合标准的国产备用设备,成本价不到30万元。
每年减少排放二氧化碳3000多吨
记者在飞华环保中央控制室内看到,一面宽大的显示屏上,实时展现着各个反应环节的运行情况,工作人员轻点鼠标,就能远程控制进料出料。
“目前,整套氯化氢废气装置的处置流程全部实现数字化、信息化管理。”侯兵说。
得益于飞华环保解决了氯化氢尾气处置难题,去年,巴斯夫又上马了MDI优化提升项目,MDI年产能提升至53万吨,实现超负荷生产。“随着巴斯夫产能不断提高,对我们尾气处置的要求也更高,这倒逼着我们去思索节能降碳,让整个过程变得更低碳、环保。”李定山说。
2022年,一场针对生产线的改造开始了。电解槽是整个氯化氢处理中的核心装置,期间,公司投资7000多万元,对电解槽进行升级改装,彻底解决了原有电解槽因使用老化而出现的槽电压不稳、阴阳离子交互效率低等问题。
在此过程中,公司又实施了数字化改造,借助传感器技术实时采集生产数据、设备运行状态、生产环境参数等信息,推动生产过程智能调控节能。
现在每个电解槽每年能节省18万度电能耗,相当于每年减少二氧化碳排放3000多吨。今年,飞华环保还将同步开展贵金属回收利用,进一步提高产业链的附加值。