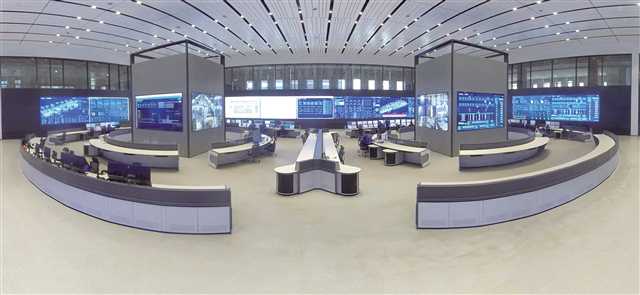 |
永锋临港钢铁基地智控中心 |
“中冶赛迪全流程智能工厂解决方案基于水土云工业互联网平台,让统一平台直接承载起各类智能应用,构建起四通八达的数据神经网络,极大地解决了协同优化困难、数据孤岛严重、数据向上大幅衰减等诸多问题。”
在2022智博会上,重庆市最大的软件企业中冶赛迪信息技术(重庆)有限公司隆重发布了一款工业智能制造产品——“冶金全流程智能工厂”系统解决方案,并介绍了中冶赛迪成功建设的首个基于统一工业互联网平台的全流程数字钢厂——山东永锋临港智能工厂,宣告中国钢铁行业已从单系统、单个生产单元的智能制造迈进全流程智能制造的新时代。
该产品在工业规模化应用中实现了钢铁生产由经验驱动向数字化智能化驱动的转变,在降本增效、精益生产、提高劳动生产率方面成效明显,并且把工人从繁重危险的劳动中解放出来,大大改善了工况环境,实现了本质安全。
在迈向“钢铁强国”的征程上,“智慧”正成为钢铁产业的鲜明特征。自2018年打造的全球首座钢铁智慧集控中心在宝武韶钢投产以来,作为钢铁智能制造领军服务商,中冶赛迪携手钢铁企业自立自强,在智能制造赛道上持续发力。2022年7月,是中冶赛迪承建的永锋临港智能工厂上线投运一年之际,作为钢铁行业首个基于统一工业互联网平台的全流程数字钢厂,凭借其良好的运行效果,备受业界瞩目。截至目前,永锋智能工厂一期工程累计上线工业模型及功能模块超过1800个,吨钢成本较本部同口径降低超过100元,人均吨钢产量超1500吨/年。该项目不仅树立了钢铁智能制造的新的里程碑,也再一次彰显了中冶赛迪在智能制造领域的行业引领者地位。
创新工业互联架构
从“智慧大脑”到“神经网络”
数据是数字时代的重要生产要素,产业领域的数据只有被收集、加工、再应用于生产实践才能创造价值。工业互联网平台是智能制造的核心底座。在传统ISA95五级信息架构中,存在纵向数据衰减和横向数据孤岛的问题。纵向上看,数据从钢铁厂自动化生产一线达到顶层集团管控,需要依次穿越多个层级,信息损耗明显,数据颗粒度越来越粗;横向上看,各个板块数据“圈地自治”,工序、部门、专业之间的数据壁垒难以打破,协同效率低下。
全流程智慧钢厂要支撑起全流程智能制造的超大规模数据应用,需要具备对全厂数据进行综合采集、无边界协同、灵活迭代拓展的能力,对传统信息架构的全面革新呼之欲出。
中冶赛迪自主研发的“水土云”工业互联网平台,打破ISA95信息化架构,采用具有自主知识产权的扁平化系统架构,让深入控制层的统一工业互联网平台直接承载起各类智能应用,很好地解决了纵向数据衰减和横向数据孤岛的问题。平台上搭载一系列核心组件,可以高效采集和处理海量数据,具备跨工序、跨系统的参数体系,让数据发挥出应有的价值。
如果说在五级架构中,信息要经过层层传达才能达到数据应用的“智能大脑”,那么“水土云”工业互联网平台就仿佛四通八达的数据“神经网络”,向上支撑全厂生产应用,向下扎根于基础自动化层面,实现全过程、全工序、全要素的数据接入和综合治理。在永锋项目中,钢铁生产全流程、全操控业务都承载于统一的工业互联网平台上,接入超过3万台工序设备,实时数据超过50万点,上线以来已累计采集、存储数据350亿条。 平台纵向打通数据传送链路,横向贯通各生产工序和管理部门,打开生产过程的“黑箱”,实现数字化透明生产,让工序之间、部门之间实现无边界协同。
操控管一体化
1800个应用模型支撑全厂数字化
只有不懈创新才能屹立于时代的潮头。从应用于韶钢的首个铁前智慧集控中心,到应用于八钢的首座热轧钢卷库智慧重载仓储系统,从应用于湛钢的首座智慧原料场、首套无人机车铁水运输系统到首个全厂智慧水控中心,中冶赛迪在推动钢铁智能制造的过程中,不断连点成线,开创钢铁全流程工艺单元的应用先河。如今,永锋智能工厂以基于统一平台的全流程智慧制造,再次创造了中国钢铁工业智能化、数字化的新样板。
永锋临港智能工厂打造了“工业互联网平台+智能管控一体化、铁区一体化、钢轧一体化”的智能工厂体系架构,使得全流程生产既能根据单元特点各司其职,又能得到贯穿全厂的统一调度。项目中,中冶赛迪开发了生产、设备、能源、物流、安环等12大类智能应用APP,配备工业模型及智能应用超过1800个,为钢铁生产从原料进厂、库存、加工到成品出厂每个生产环节都提供了数字化支撑,让操控管各环节成为统一的整体,实现全流程全厂数字化调度及各个层面的高效协同,极大地推动企业降本增效。
以温度管控为例,精准、细致的温度控制是钢铁稳定生产的基础,更是提高产品质量、提高盈利水平的重要抓手之一。项目配置的一体化管控系统可以实时跟踪高炉铁水、炼钢铁水、出钢、炉后、精炼进站、精炼出站等各个工序的物质温度情况,并基于模型预测目标温度,为铁水指吊、精炼加热升温等操作提供指导。对节奏、温度等要素的全流程管控,实现了工序界面间高效协同,系统上线后精炼电耗每吨钢降低2千瓦时,转炉和连铸平均生产周期环比分别下降1分40秒和3分2秒。
超600个实时绩效指标
透明数据支撑全员精益改善
数字化与实体经济深度融合是制造业高质量发展的必由之路。
多年来,钢铁行业发展从粗放型向集约型转变,通过管理的精细化改革和技术创新,生产效率和产品品质不断提升,但要进一步提升产品质量,降低生产运营成本,提高生产工人作业环境和效率,传统技术已难有大的成效,迫切需要全新的技术、全新的理念来推动行业进步。在新一轮科技革命和产业变革下,中冶赛迪将深耕钢铁行业60余年的领域知识与人工智能、大数据、物联网、云计算等前沿科技相结合,将智能化技术与生产场景相结合,解决了传统自动化加信息化难以根本解决的成本和效率的“天花板”问题,为钢铁行业实现更高质量的发展注入了全新动能。
“精益”一直是永锋发展历程当中的关键词之一,走过精益基础、精益运营的历史时期,进入数字化时代,永锋集团加快动能转换,与中冶赛迪携手开启“精益智能”新阶段。全流程的智能化作业不仅在操作层面提高了生产的自动化水平,还为全厂统一管控、协同联动提供了大规模的数据资产,为更好地实现精益生产打开了新的空间。
透过数据的窗口,每个员工都可以使用数据,朝着精益最优推动持续改善。传统的KPI管理往往只能管控到公司、厂部级,指标数据均为线下统计、事后测算,指标滞后且不够细化。在中冶赛迪为永锋打造的KPI看板中,指标从全厂总览逐级分解:作业区、工序、产线,直至细化到一个个班组。这套KPI管理系统配置了总计超过600个绩效指标,它们是实时计算、实时获取、实时更新的结果,不同颜色的标注让完成情况一目了然,为生产决策提供了准确、透明的数据支撑。
这是智能工厂大数据背景下全员精益的集中体现,动态化的成本控制落实到详细的责任主体。每一个员工都能在数据中定位问题,利用数据进行改善,通过持续精益改善,追求成本的极致最优。
目前,中冶赛迪业务已覆盖国内外众多钢铁企业,成为钢铁行业智能制造领域的持续领军企业,被评价为“工程设计院向智能化数字化企业转型的典范”。
周珣 陶海银 图片由中冶赛迪集团提供